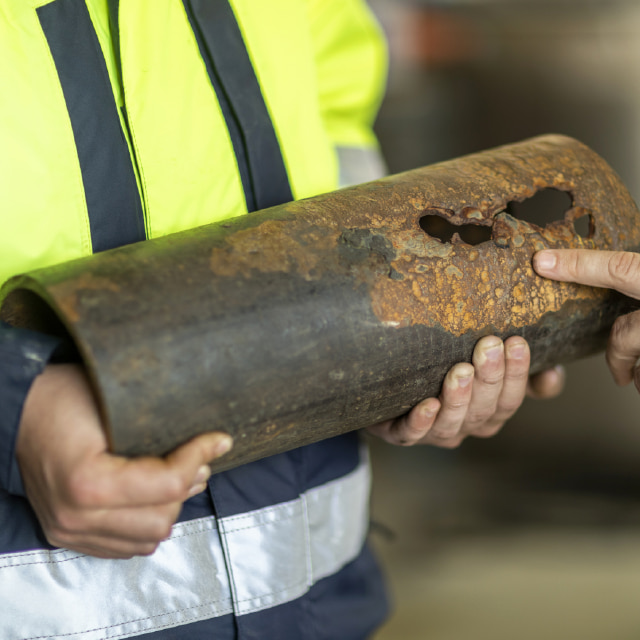
Real-life innovation
Skanderborg Utility, Denmark
A development project in close collaboration with Skanderborg Utility has provided new knowledge on the sound and noise generated by leaks and breaches in the distribution network. This has formed the basis for new and innovative leak detection in Kamstrup’s newest water meter, which Skanderborg Utility expects will create considerable value.
It started with an idea. Could the ultrasonic signal in Kamstrup’s water meter also be used to measure acoustic changes, and in that way identify leaks in the pipelines? The idea was good in theory – but it had to be tested in real life in order to ensure that it would generate value for the utilities.
”Our approach to product development has always been that a product remains unfinished until we know that it works for our customers. Innovation only becomes valuable once it has been tested in the real world,” explains Stig Knudsen, product manager at Kamstrup.

The value of collaboration
Skanderborg Utility was happy to be a part of the project, and Kamstrup applied to the VTU fund to run it as a development project, which also included Børkop Water Utility. The agreement was settled and the project kicked-of in July 2015.
”A requirement for VTU projects is that water utilities and other industry players work together, so this was a great way to organise the work,” says Stig Knudsen. Skanderborg Utility has a strong focus on collaboration and innovation, which has also led to the establishment of the AquaGlobe innovation centre, housed in Skanderborg Utility, with the mission to support the development of Danish water technology.
There was also an substantial short-term reward in participating in the project: ”In the short term, it is all about spending fewer hours tracking down leaks. We have had cases where we had to listen through a large area over the course of several weeks. We would of course like to minimise that time,” says Jens Ravn Knudsen, Head of Asset Management at Skanderborg Utility.
With the new meter, it will be easier for Skanderborg Utility to detect leaks in the distribution network. The meter will pick up any sound changes enabling the utility to narrow down the area they need to go out and investigate based on where the sound is loudest. ”The faster we can narrow down the area in which the leak might be, the quicker and cheaper we can rectify the damage instead of spending time and money on listening to an entire zone.”
Highlights from the process of creating new and innovative leak detection

Idea

Goal

Feature

Value
What does a hole sound like?
Kamstrup started with a sandbox setup in the company’s own back garden where they could test a string of prototypes. Here, the development engineers from Kamstrup and Operational Assistant from Skanderborg Utility, Frank Nielsen drilled holes in test pipes – and listened.
”We spent a lot of time filtering the sound – recognising and eliminating noise sources such as traffic, a washing machine, etc.,” explains Stig Knudsen who continues: When you have someone with years of operational experience and that mindset working together/side by side with an engineer with a Ph.D it gets really nerdy - and very productive.”
Prototypes were subsequently set up in different places around Skanderborg Utility’s distribution network – either as part of planned renovations, or in areas with suspected leakages that the prototypes then helped find.
First and foremost, Skanderborg Utility ensured that the meter was tested with the correct noise sources, but another, equally valuable contribution was their knowledge of sound and noise in the network. This was a completely new area for Kamstrup: what sound does a hole make? ”We had to learn what a leak sounds like,” explains Stig Knudsen.
Listening meetings were set up for Kamstrup and Skanderborg Utility to discuss just that, as the sound of a drilled hole is very different from the sound of a breach or leak. ”Based on our experience, we knew that drilling a clean hole in a pipe wasn’t true to life – in reality a breach is usually a tear in the pipe, which creates a more whistling sound than a round hole does,” explains Frank Nielsen.
Skanderborg Utility therefore provided Kamstrup with real pieces of piping with leak holes to investigate and test in order to learn how the type of pipe, material, composition, pressure, etc. might affect the sound of a leak. This work was crucial to the development of the new meter, explains Stig Knudsen: ”The meter listens all day, but takes the lowest background noise so we have a baseline. But when we started out, we didn’t know what to look for. Today we know what a leak sounds like.”
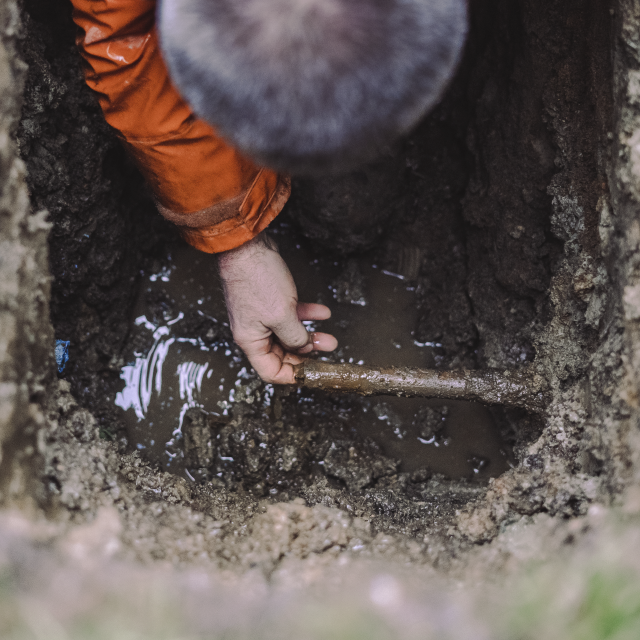
Long-term focus on asset management
Skanderborg Utility’s long-term focus is not the potential for reducing the utility’s water loss, which is already less than 6%, following a massive effort on water loss reduction in 2010. Instead, asset management is their primary focus area. Jens F. Bastrup, CEO, explains:
”For us, the greatest value will come from being at the leading edge of asset management. This will allow us to safeguard our assets and spend our money in the right places and at the right times. That is the long-term goal. If we can use data to identify the signs of an impending breach, we will essentially be able to replace the exact pipe that needs replacing – the day before it breaks.”
About AquaGlobe
AquaGlobe – Water Solution Centre – gathers the most ambitious players from the water business in order to achieve solutions that provide access to clean water and sanitation for everyone. Together, AquaGlobe's partners develop and test new, innovative and sustainable water technology directly in Skanderborg Utility's active systems.
About the project

Timeline

Meters

Yearly production
226 km of mains piping
